Ejector pin marks usually refer to the glossy or white imprints on the surface of a injection molded product, as well as the different levels of glossiness – dark or shadow, without convex or concave – visible directly opposite to the ejector pin location.
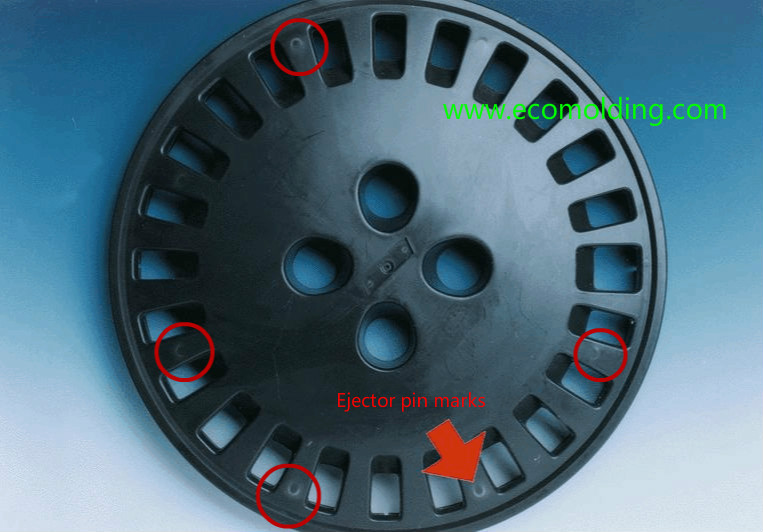
Factors that cause ejector pin mark
1. Product design:
Inappropriate product design:
1). The thickness of a product is an important factor to consider during structural design. Increasing the thickness of a product is able to not only improve the filling performance of the resin, but also reduce the orientation stress as well as product deformation. On the contrary, the excessively thin wall will make it difficult to fill the cavity, and accordingly require the increase of various molding parameters, thus making it easy to generate ejector pin marks.
2. Mold design:
1). Inappropriate gating system design: the runner is too narrow, the main runner is too long, or the runner is designed with sharp turns. All these factors will increase the flow resistance, greatly limits the filling of the plastic, and affects the adjustment of the molding parameters.
2). Inappropriate gate design: the type, location, size, and number of the gate. If the gate is too small, too much flow resistance and orientation stress will be caused. The internal stress around the gate is the highest, making the area more severely affected by stress.
3). Inappropriate ejector mechanism design: the ejector type, size, location and quantity all influence the occurrence of ejector marks, such as ribs, flanges, and bevels on plastic parts.
4). Inappropriate mold cooling channel design: the product is not evenly cooled in the cavity.
5). Inappropriate mold venting system design: when the product is in a vacuum in the cavity.
3. Machine parameters:
1). Inappropriate injection parameters: control of injection pressure and injection speed, as well as the selection of injection switching position.
2). Inappropriate holding pressure parameters: control of holding pressure and holding pressure speed, selection of holding pressure switching position, and level of backpressure.
3). Inappropriate mold temperature parameters: the different temperature settings of the mold core and the mold cavity, and the corresponding cooling channel selection for the product.
4). Inappropriate material temperature parameters: the temperature settings for each section of the barrel.
5). Inappropriate ejection parameters: the influence of ejection speed, pressure and type.
6). Inappropriate clamping force parameters: selection of machine tonnage and setting of clamping force.
Causes of ejector pin marks and solutions
1. Product design:
Whether the product wall thickness is appropriately designed is dependent on the raw material and product structure. Usually, the thickness of a simple-structured product needs to be no less than 2.5mm. Comparatively speaking, for some complex-structured products, i.e., products with more ribs in the cavity, the thickness must be no less than 2.8mm.
2. Mold design:
1). In order to save raw materials and facilitate subsequent mold changes, the sizes of the nozzle and runner are usually not too large when they are first designed. When ejector marks occur on the product, the sizes of the sprue and the runner can be appropriately increased to alleviate the overshooting of the injection pressure and other parameters caused by filling difficulty (note: the sizes of the sprue and the runner can only be changed and increased when the injection parameters are too high, or other severe issues may occur; design vents at the runner end). The internal stress around the gate is the highest, so the gate should be located where it is easy to fill the cavity and as far away as possible from the ejector, while resin filling should be as uniform as possible to ensure uniform stress distribution.
2). The type, arrangement, size, location and number of ejectors all have a lot to do with the occurrence of ejector marks. The design should ensure that the properly sized ejector pin is uniformly stressed when the product is ejected. For example, the areas with deep ribs, that is, the areas where it is more difficult to eject the product, need to be ejected with higher force. Also, the ejector pins need to be designed on the ribs.
For products with deep ribs, it is necessary to put the stress points on those deep ribs, so as to avoid ejector marks caused by excessive force during product ejection.
The design of the ejector pin location should take the following two factors into consideration: whether it is ejected at the maximum stress point and whether it is balanced.
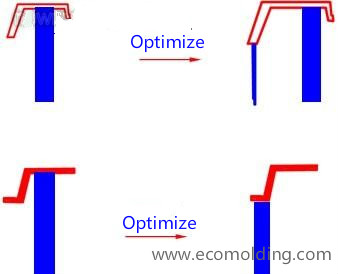
3. Machine parameters:
1). Selection of injection molding machine: Inappropriate selection of injection molding machine will also lead to the generation of internal stress. The idea that a large-capacity injection machine injects products with a small mold will reduce internal stress is incorrect. Sometimes large internal stress is caused by excessive pressure and inappropriate nozzle structure.
2). Molding process conditions: Due to the characteristics of the molding process, ejector marks are inevitable on molded products, but the appropriate control of process conditions is able to minimize them; the factors that influence the occurrence of ejector marks include mold temperature, processing temperature, injection speed, injection pressure, holding pressure, injection time, pressure holding time, and cooling time, etc., among which, temperature, pressure, speed and time constitute the main factors of the plastic injection molding process.
3). Processing temperature
4). Injection pressure, speed and time
5). Holding pressure and holding time: For holding pressure, when the product is more than 90% injected, use this parameter to adjust it. Sometimes, reducing the holding pressure and the holding time is able to reduce the orientation stress. At this point of time, you will find that ejector marks are actually much improved.
6). Insufficient cooling time. When the product is ejected before its surface temperature reaches the highest ejection temperature of the plastic material, ejection defects such as convex or penetration are prone to occur.