Definition of Flow Lines:
Flow lines, also known as flow marks Linear marks on the surface of a molded product, which indicates the flow direction of the molten plastic.
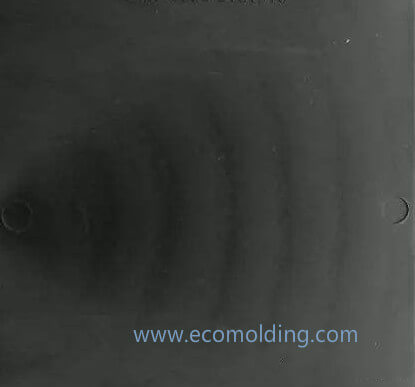
Injection Molding process
1.Insufficient Pressure / Holding Pressure
The injection pressure and the holding pressure are not high enough to press the solidified layer against the mold surface, thus leaving flow lines along the melt flow direction.
Increase the injection pressure and the holding pressure, to press the solidified layer against the mold surface until the product is molded, so as to prevent the occurrence of flow lines.
2.Improper Residence
Time
The plastic material stays in the barrel for a too short period of time, while
the melt temperature is low. Even if the cavity is barely filled, the plastic cannot
be compacted during pressure holding, thus leaving flow lines along the melt
flow direction.
The Shot-to-Barrel Ratio should be kept
between 1/1.5 and 1/4.
3.Improper Cycle Time
When the cycle time is too short, the plastic is not sufficiently heated in the
material barrel, and the temperature of the melt is low. Even though the cavity
is barely filled, the plastic cannot be compacted during pressure holding, thus
leaving flow lines along the melt flow direction
The cycle time is extended until the plastic is fully melted, and the temperature of the melt is high enough to prevent flow lines along the melt flow direction.
4.Barrel Temperature Too Low
When the barrel temperature is too low, the melt temperature will be low, and the injection pressure and holding pressure will not be high enough to press the solidified layer against the mold surface, thus leaving flow lines along the melt flow direction.
Increase the material temperature, injection pressure and holding pressure to press the solidified layer against the mold surface until the product is molded, so as to prevent the occurrence of flow lines. The material temperature can be set by reference to material supplier’s recommendations.
The material barrel is divided into four zones: Rear, Center, Front and Nozzle. The material temperature settings should be gradually raised as it moves forward. Increase by 6°C with every zone forward.
When necessary, the temperature of the Nozzle and/or the Front are sometimes set to be the same as the Center temperature.
5.Nozzle Temperature Too Low
After absorbing the heat released by the heating band, as well as the frictional heat generated by the relative movement of the plastic molecules caused by the rotation of the screw, the plastic in the barrel undergoes gradual temperature rises.
The last heating zone in the barrel is the Nozzle, where the melt should reach the desired temperature, but it must be moderately heated to maintain the optimal conditions.
If the nozzle temperature is not set high enough, due to too much heat is taken away through the contact between the nozzle and the mold, the material temperature will decrease, so that the injection pressure and the holding pressure will not be high enough to press the solidified layer against the mold surface, thus leaving flow lines along the melt flow direction.
Raise the Nozzle temperature. The nozzle temperature is usually set to be 6°C higher than the Front temperature.
Mold
1.Mold Temperature Too Low
If the mold temperature is too low, the material temperature will drop very fast, so the injection pressure and the holding pressure will not be high enough to press the solidified layer against the mold surface, thus leaving flow lines along the melt flow direction.
Raise the mold temperature, maintain a high material temperature, as well as high injection pressure and holding pressure to press the solidified layer against the mold surface until the product is molded, so as to prevent the occurrence of flow lines.
The mold temperature can be set from the recommended values of the material supplier, with an increment of 6°C at each adjustment. Then perform 10 shots, and after the injection molding is stable, decide whether further adjustment is necessary according to the result.
2. Sizes of the Sprue, the Runner and/or the Gate
If the sprue, the runner, and/or the gate are too small, the flow resistance will be increased. And, if the injection pressure is not high enough, the advancement of the melt front will become slower and slower, and the plastic will become colder and colder, so that the insufficient injection pressure and holding pressure will not be able to press the solidified layer against the mold surface, thus leaving flow lines along the melt flow direction.
It is a feasible way to simulate and analyze the filling status of the different melt transfer systems (including the sprue, the runner and the gate) on a computer with CAE (such as, C-MOLD), to find out the ideal sprue, runner, and gate sizes (including length and section related dimensions, such as diameter, etc.)
3. Insufficient Venting
Insufficient venting will cause the melt filling to be blocked, and the melt front will not be able to press the solidified layer against the mold surface, thus leaving flow lines along the melt flow direction.
Start venting at the end of each runner section, which removes a large amount of gas before filling the cavity.
The cavity venting should not be neglected. Consider adding vents on the parting surface opposite to the gate. Correspondingly, consider adding venting ejector pins at the end of the product blind hole.
Simulate melt filling through CAE (such as, C-MOLD), which helps us quickly find out all possible last filled areas, i.e., the areas where vents must be added. The addition of a vacuum system for air extracting before and during filling is an effective venting method.
For some textured products, this may be the only way of venting.
Plastic Material
1.Poor Fluidity
The mold cavity with a large flow length to thickness ratio must be filled with the plastic that features great fluidity. If the fluidity of the plastic is not good enough, the melt will be flowing slower and slower, colder and colder, so that the injection pressure and the holding pressure are not high enough to press the solidified layer against the mold surface, thus leaving flow lines along the melt flow direction. Material suppliers are able to offer professional recommendations according to specific designs:
The most flowable plastic is selected on condition that no flashing is caused.
2.Improper Application of Molding Lubricant
Usually, the lubricant content is below 1%. When the flow length to wall thickness ratio is large, the lubricant content must be moderately increased to ensure that the solidified layer is pressed against the mold surface until the product is molded, so as to prevent the occurrence of flow lines. The lubricant must be increased upon agreement with the material supplier.
Operator
1. Bad Habits
Inconsistent molding result will occur if the operator switches the door of the injection molding machine too early or too late. When the barrel heater tries to replenish heat in time due to irregular heat loss, the plastic temperature will not be uniform, thus causing the cold spot. It is not easy for the injection pressure and the holding pressure to press the solidified layer around the cold spot against the mold surface, thus leaving flow lines along the melt flow direction. Usually, the operator should be constantly educated to let everyone know the troubles caused by inconsistent molding cycles and recognize the importance of maintaining best molding practices. Appropriate work shifts are able to prevent operators from making mistakes due to exhaustless or distraction. Automated production with robots or the like is a way to maintain a consistent molding cycle.