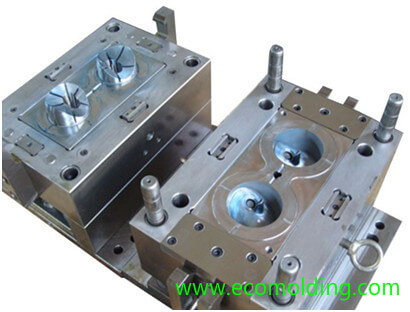
When compared with other tools, the plastic injection mold is more complicated and precise, with higher requirements for operation and maintenance. As a result, throughout the entire production process, their correct use and meticulous mold maintenance are of great significance to maintain the normal production and improve the efficiency of a company.
1. Select the right molding equipment, and determine the reasonable process conditions. If the injection molding machine is too small, it will not meet the requirements; if too large, it will waste resources. Also, it may damage the mold or the mold plate due to the improper adjustment of the clamping force, while at the same time affecting the production efficiency.
When selecting the injection molding machine, check the maximum injection volume, the effective distance of the tie rod, the mold installation dimensions on the plate, the maximum mold thickness, the minimum mold thickness, the plate stroke, the ejection type, the ejection stroke, the injection pressure, and the clamping force, etc. and choose the one that meets the requirements. The reasonable determination of the process conditions is also one of the factors that ensure the correct use of the mold. If the clamping force, the injection pressure, the injection speed and the mold temperature, etc. are set to be too high, the service life of the mold will be affected.
2. After installed with a mold, the injection molding machine must first be operated with the empty mold, to observe whether the operation of each part is smooth, whether there is any anomaly, whether the ejection and opening strokes are proper, whether the parting surface is tightly matched when the mold is closed, and whether the pressure plate screw is tightly fastened.
3. When the mold is being used, a normal temperature should be maintained to help extend the service life of the mold.
4. Sliding parts on the mold, such as the guide pin, the return pin, the push rod and the core, etc., should be inspected, cleaned and lubricated regularly. Especially in summer when the temperature is high, add lubricants at least two times per shift, so as to ensure that these sliding parts are smooth enough to prevent seizures.
5. Each time before closing the mold, check whether the mold cavity is cleaned or not – no residual products or any other foreign objects are allowed. It is strictly forbidden to use hard tools to clean the cavity, so as to prevent the cavity surface from being damaged.
6. As for molds with special requirements for the cavity surface, the surface roughness (Ra) should be no higher than 0.2cm. It is absolutely not allowed to wipe it with hand or cotton fabrics. Instead, it should be cleaned with a compressed air blower, or gently wiped with high-grade alcohol napkins or absorbent cottons.
7. The cavity surface should be cleaned regularly. During the injection molding process, the mold will produce low molecular compound to corrode the mold cavity, so that the surface of the glossy cavity gradually becomes matted, thus affecting product quality. Therefore, it needs to be cleaned regularly by using alcohol or ketone preparation before being dried in a timely manner.
8. When the machine needs to be temporarily stopped, the mold should be closed to prevent the cavity and the core from being exposed, which might create accidental damage. If the downtime is expected to exceed 24 hours, the surface of the core and the cavity should be sprayed with anti-rust oil or release agent. Especially in moist areas and rainy seasons, they should be rust-proofed even if the downtime is very short. The moisture in the air will affect the surface quality of the cavity and the molded product. Before the mold is put into operation again, the oil on the mold should be removed and wiped clean. When cleaning a mold with mirror surface requirement, first use compressed air and then hot air to dry it, or the oil will be oozing out to cause product defect during the molding process.