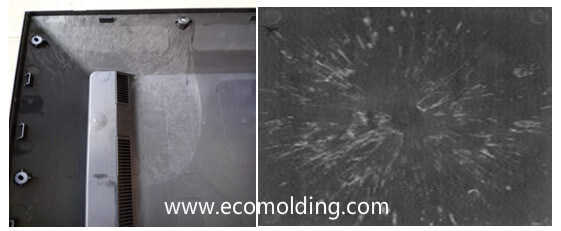
Definition of silver Streaks:
Silver streaks are also referred to as silver marks, which appear like burst blisters on the surface of injection molded parts, mostly in the shape arrows pointing to the gate.
Causes of Silver Streaks:
I. Equipment
1. The nozzle hole is too small, the material leaks or draws at the nozzle, or the barrel or the nozzle is obstructed, and the material decomposes due to the frictional heat caused by high-speed melt flow;
2. The barrel and the screw wear, or melt flow dead ends exist in the screw cap and collar, which are decomposed due to long-time heating.
3. The heating system is out of control, causing the temperature to be too high and resulting in decomposition. Check whether there are any problems with the heating elements such as thermocouples and heating coils. Improper screw design also leads to decomposition or brings in air.
II. Mold
1. Due to design defects, such as poor gate location, too small gate, asymmetrical gate deployment, small runner, and improper mold cooling system, the mold temperature varies a lot, so the melt doesn’t flow smoothly in the cavity, which blocks the passage of air.
2. The corners are too sharp, and the shear force is too large when the melt passes by, thereby causing the occurrence of silver streaks;
3. The mold parting surface is designed with no or insufficient vents, or the vents are blocked or inappropriately placed, with no clearances or gaps for venting, such as inserts and pins, so that the air in the cavity cannot be vented when the melt flows in.
4. A rough mold surface creates a higher frictional resistance, causing local parts to be overheated, which decomposes the passing plastic.
5. The mold leaks oil, water, and air into the mold cavity, which easily causes silver streaks on the part surface.
III. Molding Process
1. The material temperature is too high, which causes decomposition. If the barrel temperature is too high or the heating is imbalanced, the barrel temperature should be lowered step by step. If the temperature of the feeding section is too high, part of the plastic will melt prematurely and fill the groove, making it impossible to vent the air through the feeding port.
2. When the injection speed is too fast, the molten plastic will be decomposed by the large shear force, and gas is accordingly generated; if the injection speed is too slow, the product cannot be filled in time, causing an insufficient surface density, and thus the silver streaks.
3. Insufficient material, too large feeding buffer, too low material temperature or too low mold temperature will affect the fluidity and molding pressure of the melt, and thus generate voids.
4. During pre-molding, if the screw backpressure is too low and the speed is too high, the screw will return too fast, so that the air is easily pushed to the front end of the barrel together with the material.
IV. Material
1. A large amount of dust is mixed into the raw materials or mixed with the pellets, which is easy to entrain air during the melting process, and sometimes silver streaks are caused. When the raw materials are contaminated or there is too much dust, the raw materials are easily decomposed when being heated.
2. Too much sprue (recycled material) is added, the sprue is recycled for too many times, or a too high proportion of sprue is mixed with the new material (usually no higher than 20%).
3. The additives in the material decompose to generate silver streaks.
4. Excessively moist materials are not fully dried, resulting in silver streaks.
5. The material contains a high water content or is porous, which causes the silver streaks on the molded part.