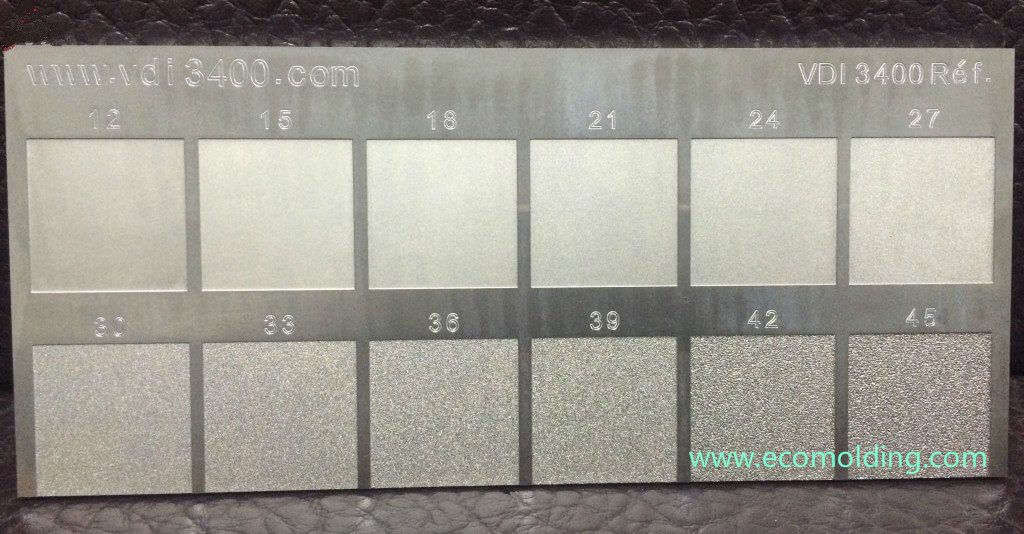
Different physical and chemical properties of the polymer blends, as well as the different parameters of the plastic injection molding process cause the surface finish on the plastic composites to vary greatly.
For a plastic injection molding service provider that offers custom-made products, the first goal is to work in collaboration with the client to determine the importance of surface finish for the exterior appearance, as well as the performance of the injection molded product, or to be specific, is the final product an eye-catching piece or simply a functional one? Your answer to this question determines the choice of material and the option of surface finish, based on which the plastic injection molding process is set, and the secondary finishing operations are accordingly required.
Available Surface Finish Types
Before making your final decision on the surface finish type for your plastic injection molded product, you should first have a clear idea in mind of what type of mold you need on the basis of your production volume, as well as the type of the material that your mold is going to be made of. Usually, a steel mold is of a higher hardness than an aluminum one, thus able to offer more surface finish options, because the steel material possesses the benefit of being able to be polished for a surface finish that is smoother than other materials, which is also helpful for such secondary finishing operations as painting aimed to enhance your final molded products.
Available surface finish types include:
- Geometric shapes / patterns
- Grains, e.g., the leather texture
- Secondary finishes, e.g., paintings, print, etc.
- Etching
- Sand blast
- Glossy, matte, or satin finishes
- Mirror polishing or lens finishes
CATEGORIES of SURFACE FINISH
The Society of the Plastics Industry (SPI) has standardized the surface finishes for plastic injection molds. According to the finishing process selected, the following grades are determined:
Finish | SPI* standard | Finishing Method | Typical surface roughness Ra (μm) |
Super High Glossy finish | A-1 | Grade #3, 6000 Grit Diamond Buff | 0.012 to 0.025 |
High Glossy finish | A-2 | Grade #6, 3000 Grit Diamond Buff | 0.025 to 0.05 |
Normal Glossy finish | A-3 | Grade #15, 1200 Grit Diamond Buff | 0.05 to 0.10 |
Fine Semi-glossy finish | B-1 | 600 #Sand Paper | 0.05 to 0.10 |
Medium Semi-glossy finish | B-2 | 400# Sand Paper | 0.10 to 0.15 |
Normal Semi-glossy finish | B-3 | 320#Sand Paper | 0.28 to 0.32 |
Fine Matte finish | C-1 | 600 Grit Stone | 0.35 to 0.40 |
Medium Matte finish | C-2 | 400 Grit Stone | 0.45 to 0.55 |
Normal Matte finish | C-3 | 320 Grit Stone | 0.63 to 0.70 |
Satin Textured finish | D-1 | Dry Blast Glass Bead #11 | 0.80 to 1.00 |
Dull Textured finish | D-2 | Dry Blast #240 Oxide | 1.00 to 2.80 |
Rough Textured finish | D-3 | Dry Blast #24 Oxide | 3.20 to 18.0 |
Machined Marks | – | – | 3.20 (with visible machining marks) |
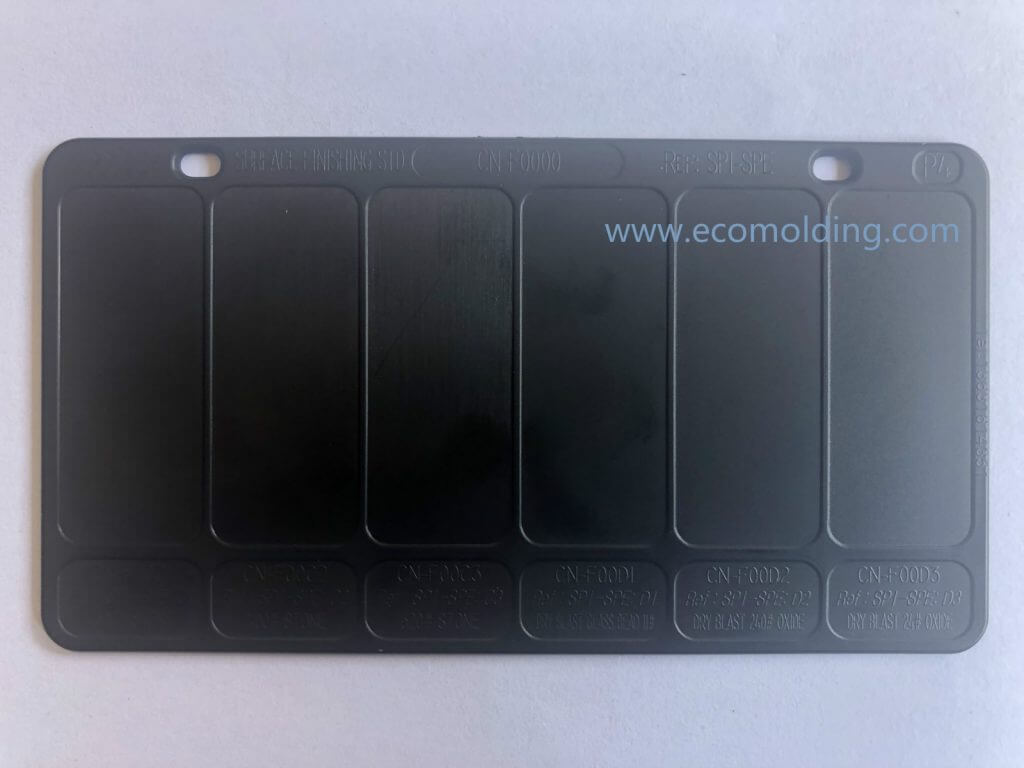
AESTHETICS or FUNCTIONALITY
In surfacing finishing, a balance needs to be achieved between aesthetics and functionality, because the surface finish is able to affect not only the friction coefficient, but also the resistance to wear and tear; if these are considered to be important characteristics for the product performance, the design team is then required to choose the material and process that helps create a well matched finish effect. A skilled plastic injection mold maker is equipped with tremendous scientific data with regard to material chemistry, material behavior, and process conditions, so as to get the reference for accurate choice of surface finish process on the basis of specific parameters.
It is of critical importance to decide the surface finish type as early as the design stage, because it has a great influence on your selection of material and tooling, as well as your choice of the finishing process. The surface finish of a product is limited by the textures on the tool steel. From time to time, the imperfections, such as sink mark, on a surface can be covered by a rougher texture pattern. In addition, the draft required on a molded part can also be affected by the surface finish – if the draft is not appropriately designed, the surface finish could probably be destroyed during the ejection process.
SELECTION of PLASTIC MATERIALs
Your choice of the material, the additive, and the different plastic injection molding parameters, such as the fill rate, as well as the injection pressure and temperature affects the 2 key surface characteristics of glossiness and roughness. What is of special importance is the type of the material, e.g., the higher the melt temperature of the products made from reinforced crystalline resins, the more glossy and less rough the surface is, thus creating a smoother effect. However, when being plastic injection molded, a higher mold temperature is able to improve the glossiness and reduce the roughness of the reinforced amorphous resins.
Also, with regard to surface finish, another critical consideration is the additive that is applied to the resin material. At this point, the knowledge of material science is truly brought into play, e.g., the addition of contents containing fiberglass will lead to a lower glossiness. On the other hand, such additives as the carbon black and mica are able to reduce surface roughness, meaning if you have to maintain a certain degree of surface roughness out of considerations for product performance or appearance, you need to avoid or at least find substitutes for these additives. Also, if you add particulate fillers, the surface roughness might be increased. To produce a specific surface finish, a qualified engineer should be able to mix and match the proper combination of resins with additives.